Executive Summary
- Recent global events have emphasized the need for reviewing and strengthening the supply chain for manufacturers from both an operational and cost savings perspective.
- A “China Plus One” strategy is a good start but may prove inadequate depending on the nature of a disruption.
- Supply chain backup plans need to be agile, flexible, and built with contingencies for undetermined issues.
- Raising prices may address some concerns but also causes customer issues and is not a long-term solution.
During the COVID-19 pandemic, organizations across different trades and industries faced a number of operational obstacles caused by supply chain disruptions. From economic uncertainty, to labor shortages, to rising costs, leaders had to find alternatives to create an agile and adaptable framework for this ever-changing market. With the global tax overhaul where juristidictions are racing for the middle and not the bottom, companies are faced with continuous change.
Our International Tax and Transfer Pricing leaders have developed methods and problem-solving techniques for local and global networks. These approaches help businesses address their supply chain challenges, as well as give guidance on how to continually evaluate and adjust their strategic initiatives while considering tax and transfer pricing risks in their supply chain decisions. The proverbial tax tail should not wag the dog but it should not be ignored either. Companies should consider performing transfer pricing analyses to determine how to allocate the financial impact of the changes to the supply chain among related entities and ensure appropriate remuneration to those entities involved in supply chain initiatives for their respective functions performed and risk incurred in the process.
In this article, we will answer three of our most-asked questions and provide the necessary steps to transform and optimize supply chains amid constant uncertainty — now and in the future.
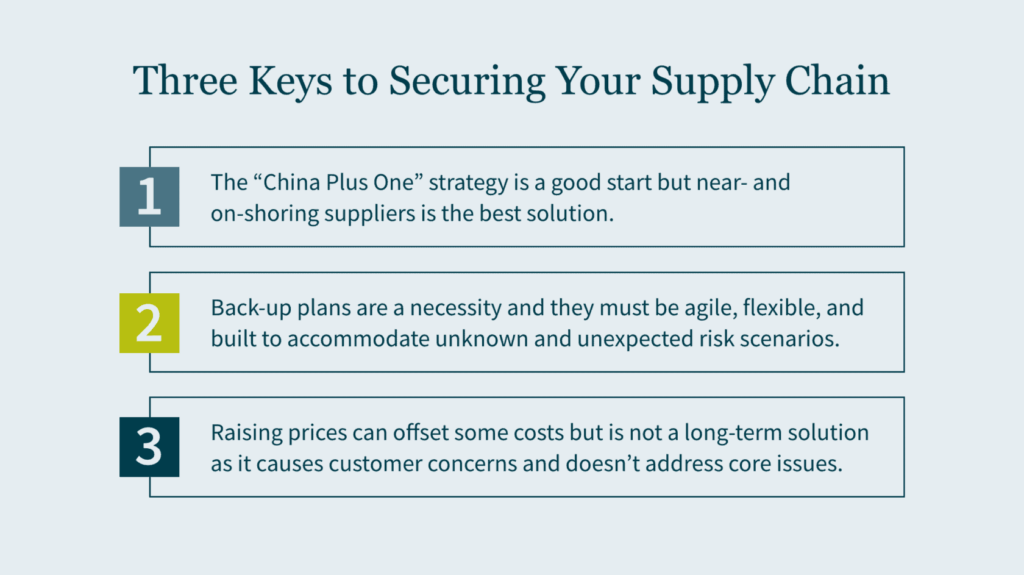
#1: Can adopting the “China Plus One” strategy diversify my supply chain?
In recent years, most U.S.-based businesses and consumers have learned that global supply chains have become too dependent on China. Prior to 2020, business leaders had already begun shifting away from China in the wake of the previous administration’s tariff challenges, intangible property (IP) disputes, and the ensuing trade war. Factory and port shutdowns in China in the early days of the pandemic and the issues that have followed were wakeup calls for those that hadn’t implemented alternative sources of supply. An enduring lesson of the past few years is that sole sourcing from any vendor or vendors in one location comes with a high-risk level. In renewing the supply chain, companies must consider the economic climate, the political environment, the ease of doing business, and personnel availability. Tax and transfer pricing is generally not in the forefront nor should it be. But giving it some thought after consider the already mentioned items may pay significant dividends.
Building redundancy into the supply chain at different tiers and maintaining inventory levels have become necessary steps for international manufacturers.The China Plus One strategy has been on the radar of companies that operate in China for several years, but the need to diversify supply chains is now a priority, with many manufacturers actively pursuing supplementary sourcing from another country in Southeast Asia. However, the supply chain crisis of the past two years shows this strategy may also be failing. As long as the goods produced are an ocean away from the markets that consume them, uncertainty from various disruptive factors can lead to shortages, higher costs, lower revenues, and customer dissatisfaction.
Actions moving forward:
Along with decoupling from China, truly de-risking the supply chain comes down to three factors:
- Optionality
- Redundancy
- Market proximity
While fully onshoring production and supply sources may not be operationally, economically, or logistically feasible, the supply network is less risky when it is closer to the market where it is widely consumed.
Consider engaging or contracting new stateside suppliers and local manufacturers to better serve the U.S. market. You should also review your supply base for any overreliance on a single source or geography. After that, you can research the best options to decrease the distance between where your products are produced and purchased. Insourcing, onshoring, nearshoring and acquisitions are all viable options. The approach that makes sense for your business must consider cost, capacity, quality, control, and reputation. Regardless of your approach, the goal should be to improve supply chain resilience and flexibility so you can better manage disruptions.
#2: Does having a back-up plan reduce supply chain disruptions?
Preparation and readiness may help with how your company fares during industry interruptions. A back-up plan should have built-in agility so it can be adapted and activated quickly based on a variety of external factors.
In recent years, manufacturers learned static backup plans were not adequate to address rapidly changing global conditions. These backup strategies were not agile enough to be effective amid complex disruption. Consequently, manufacturers were challenged to get the level of service they needed from existing suppliers or quickly identify new suppliers, resulting in processes that simply were not feasible from an implementation or sustainable cost standpoint.
Backup plans are a necessity, but they’re generally based on known risks. As global supply chains grow more intertwined and the universe of uncertainty expands, new risks and variables come into play. You can’t just plan for one contingency; you need to weigh the possible outcomes for multiple options across different scenarios. Changes in manufacturing locations and sourcing strategies aren’t the only scenarios worth evaluating, nor is resilience to disruption the only outcome worth measuring. For example, if you’re considering expanding into a new market or adding to your product mix, those strategic adjustments should be factored into your supply chain model and assessed for plausibility. Tax liabilities, trade compliance risks, and total cost to serve are no less critical considerations than deliverability or lead times.
The reality is you cannot prepare for every contingency, so scenario planning needs to evolve to detect signals of disruption earlier and enable greater agility in supply chain decision-making when the unexpected occurs. For example, if your company is planning on vertical integration thath will be the cause of significant in-country hiring, you must assess the benefits of employment credits and incentives that can help reduce overhead costs.
Actions moving forward:
Review your supply chain model to:
- reflect current constraints;
- incorporate points of vulnerability; and
- conduct a scenario planning exercise to address a specific problem or inform your next strategic move.
Ideally, you should simulate multiple scenarios to pressure test the supply chain, anticipate issues, and chart the best path forward when disruption hits. Scenario planning should become a regular business practice so you can quickly respond to unforeseen events.
#3: Will raising prices offset the increasing costs of materials and logistics?
Although raising prices is not the only way to successfully reduce costs, there are some tradeoffs that will have to be considered. Higher costs are an unfortunate reality for most manufacturers in the current supply chain environment. Because cost reductions are not easy to accomplish, many companies are shifting their focus to cost containment within areas of their supply chains that they can control. Higher costs are a sure way of reducing taxable income and where possible, selectively deciding where the spend will occur in the supply chain may not reduce the impact of inflation or costs being spent – however it may impact the amount of tax dollars being spent. Tax, like all other costs, is an expense that should be viewed and considered for cost reduction measures.
For example, intercompany movements are often rife with inefficiency or seldom get the level of scrutiny they deserve. If parts and finished goods are shipped intercompany, ask why: Is there a value add, is it because your business has always done it that way, or is it an enabling factor to hedge against process inefficiencies? If your global supply chain is failing to consistently meet the needs of local markets, does the original rationale for keeping production and sources of supply at a distance still stand? Or would it be beneficial to establish a near or local market capability? Using models like a contract manufacturer can be a quicker way to further evaluate whether it makes sense to establish an in-house capability.
It’s also a good time to revisit lean initiatives that you may have previously dismissed or deprioritized—though be cautious of prioritizing efficiency at the expense of resilience. And beyond your own four walls, there are a few foundational measures of good supply chain hygiene that may help with cost takeout:
- Shift from transportation spot rates to contract rates to stabilize pricing.
- Ensure you have contracts with alternate suppliers; don’t rely on a single source.
- Encourage your customers to optimize order volume for full truck or container loads through more rigorous enforcement of transactional service standards.
These measures may help manage costs to some degree but are unlikely to completely offset them. By raising prices, you will more than likely create frustration and confusion among your customers. However, if you find yourself absolutely needing to raise prices, it’s better to be upfront and honest rather than taking a below-the-radar approach.
Another way to address rising costs, rather than passing additional costs onto all your customers, is to consider segmenting them and developing pricing strategies based on level of priority.
Actions moving forward:
Perform an in-depth analysis of your customer base and product suite to understand the most and least profitable segments. Consider implementing a price segmentation strategy that shifts the heaviest burden of cost increases to your least profitable customers. Also, take a close look at your least profitable product segments and how they line up with cost distribution. Do you have slow-moving SKUs driving a disproportionate amount of costs? It may make sense to rationalize them.
We can help strengthen your supply chain
Now is the perfect time for manufacturers to gain competitive advantage by optimizing production and delivery processes and prioritizing long-term spending goals. Our International Tax and Transfer Pricing and Management Advisory practice leaders are ready to assess your current supply chain, identify potential points of weakness, adjusting transfer pricing policies, and assist you in implementing strengthening procedures. Reach out to our team to learn how we can reduce your risk and power production.